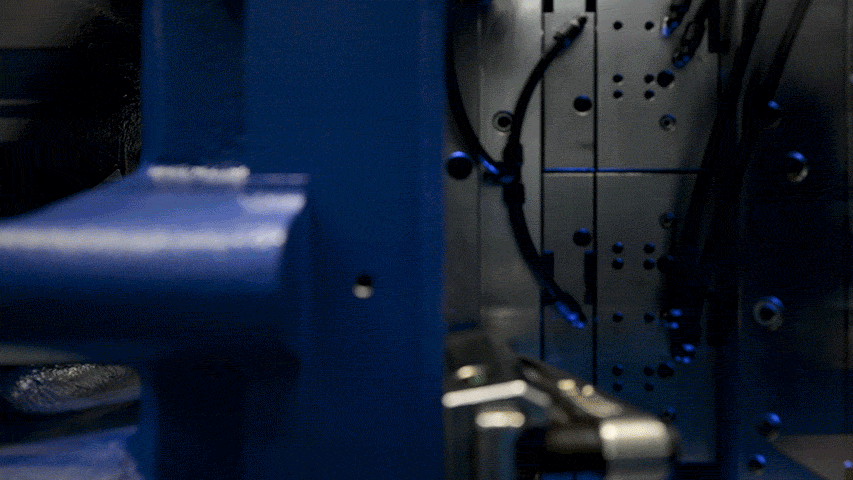
We recently wrote a blog post about the 8 Key Parameters in Injection Molding Process Optimization to Avoid Defects, but there was one that we didn’t mention: clamp force. Clamp force and geometry play a pivotal role in the injection molding process and can greatly impact how efficient (or not) a process is. In this blog, we will discuss what clamp force is, why proper clamp force matters, what clamp geometry is, and the importance of optimal clamp geometry.
What is Clamp Force?
Clamp force refers to the force applied to the mold halves in a plastic injection molding machine to keep them securely closed during the injection phase. It is the force required to resist the pressure exerted by the molten plastic material as it fills the mold cavity. Proper clamp force ensures that the mold remains tightly sealed, preventing issues like flash, where excess plastic escapes from the mold, and maintaining dimensional accuracy in the final product.
The Significance of Proper Clamp Force:
- Preventing Part Distortion: Insufficient clamp force can lead to part distortion as the mold may not be able to withstand the pressure of the injected plastic. This can result in part variation and scrap.
- Prolonging Mold Life: Adequate clamp force is crucial for extending the life of the mold. Properly clamped molds experience less wear and tear, reducing maintenance and replacement costs.
- Minimizing Flash: Maintaining the correct clamp force helps prevent flash, which occurs when molten plastic escapes from the mold cavity. Flash not only wastes material but can also lead to scrap, additional steps to remove the excess material, or shipping bad parts.
- Ensuring Consistency: Consistent clamp force is essential for achieving uniformity in the molded parts. It helps in producing identical components with minimal variations, meeting stringent quality standards.
- Maintain Proper Venting: When the mold closes, air is trapped inside the cavity. Vents allow this air to escape but are too small for plastic to fit through. Proper clamp force ensures these tiny vents are not crushed under too much pressure. If that does happen, you end up with either a burn (the air compresses under pressure and creates a dieseling effect) or a non-fill (the plastic cannot fill the space of the cavity occupied by trapped air).
What is Clamp Geometry?
Clamp geometry refers to the design and configuration of the mold and the clamping system. It includes factors such as the mold’s shape, size, and the arrangement of the clamping components. The geometry of the clamp influences how evenly the force is distributed across the mold, impacting the overall performance and longevity of the injection molding process. If moving a mold from one machine to another, clamp geometry, especially between toggle and hydraulic clamps and machines with different tie bar spacings, can influence part geometry and surface finish of parts produced.
The Importance of Optimal Clamp Geometry:
- Uniform Force Distribution: Well-designed clamp geometry ensures that the applied force is distributed uniformly across the mold surface. This helps in preventing uneven pressure points, which could lead to mold deformation or premature wear.
- Reducing Stress on Mold Components: Proper clamp geometry minimizes stress on critical mold components, such as guide pins and ejector pins. This, in turn, extends the life of these components and reduces the likelihood of production interruptions.
- Enhancing Cooling Efficiency: Efficient clamp geometry facilitates optimal cooling of the mold to maintain cycle times and achieve consistent part quality.
- Accommodating Complex Molds: Complex molds with intricate designs and multiple cavities require careful consideration of clamp geometry to ensure that the mold can be securely closed without compromising the integrity of the final product.
Conclusion:
In plastic injection molding, the combination of clamp force and clamp geometry is a critical factor in maintaining effective and efficient processes. Achieving the right balance ensures the production of high-quality, dimensionally accurate plastic parts while maximizing the life of the molds.
What’s Next?
Want to learn more about clamp force and optimizing your injection molding process? Check out our upcoming training courses!