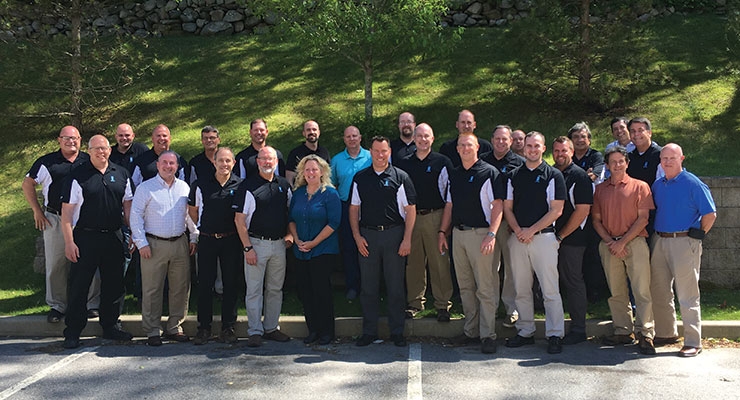
In May of 2016, the Medical OEM Consortium (MOEMC) formed. A group of original equipment manufacturers (OEMs) set out to discover a more efficient part validation process for injection molding. They executed and formally documented their results. By creating a “Part Process”, molders are able to replicate transferable plastic conditions that eliminate the need to 100% re-validate the tool every time it is moved to a new machine. This new technique has the potential to save molders millions of dollars and thousands of hours of inefficient downtime annually.
Today, the findings from the proof of concept are officially released in the format of a technical white paper, available for download on RJG’s website. The white paper, entitled “Part Process” Transferability Using a Machine Independent Variable (MIV) Methodology for Multiple Machines, walks through the methods, materials, results and conclusions of the Consortium’s research. Through the execution of this discovery exercise, the MOEMC has provided a broadened perspective on the acceptance of the “part process” method to allow the transfer of molds in the medical device industry as a practical alternate standard.
Traditionally, a part must be re-validated every time the mold is going to run in a different machine, especially in high precision applications that are found in medical devices. This costs millions of dollars a year and leads to weeks or months of machine downtime, leading to lost revenue for both the OEM and molder. By creating a process that can be successfully transferred from machine to machine based on a reduced verification run, molders can save millions and greatly reduce or eliminate machine downtime. Also, there is an increased assurance that the methods used can help reduce and mitigate risk based on data-driven decisions (using available technology) that can help drive continuous improvements and sustain the required statistical control.
“This is the future of Medical Molding,” said Scott Scully, Director, Corporate Molding/Tooling at Terumo Cardiovascular Systems. “For too long, the cost of full validation to move a mold has kept the industry handcuffed and has thwarted OEMs to move quickly on unexpected schedule demands. To remain competitive, we must change to validating the ‘Part Process’ instead of the ‘Machine Process’. Those who do will out-compete those who don’t.”
“What was amazing to watch was that the SQE/Quality Team really engaged to learn about the molding process and understand its effect on the dimensional results,” said Matt Therrien, Business Development Manager at RJG. “At the end of the Consortium, they were the most passionate about explaining the benefits of the newfound data-driven approach.”
”Over the past 15-20 years, the injection molding industry has experienced amazing progress in process technology,” said Paul Robinson, Lead QA/RA Compliance Consultant at Quality System Consulting Services (QSCS). “The ability to model, monitor and control injection molding has improved exponentially. As a result, I recommend looking for opportunities to drive efficiency by taking a hard look at some of the examples of reasons for revalidation in section 6.4 from GHTF/SG3/N99-10:2004 (Edition 2) Quality Management Systems – Process Validation Guidance:
“The need for revalidation should be evaluated and documented. This evaluation should include historical results from quality indicators, product changes, process changes, changes in external requirements (regulations or standards) and other such circumstances.
“Revalidation may not be as extensive as the initial validation if the situation does not require that all aspects of the original validation be repeated. If a new piece of equipment is purchased for a validated process, obviously the IQ portion of the validation needs to be repeated. However, most of the OQ aspects are already established. Some elements of PQ may need to be repeated, depending on the impact of the new equipment.”
Abstract:
In the medical device molding industry, manufacturing plastic parts in multiple machines requires expensive and time-consuming validations for each injection molding machine (IMM). Here we employ a Machine Independent Variable (MIV) method to effectively and efficiently transfer a validated “part process” across four distinctly different IMMs. Critical to Quality (CTQ) results for each transfer were required to meet Ppk targets to match the CTQs of the initial validation. Our results show the MIV transfer method, verified with eDART® technology, can be used to replicate plastic parts in different IMMs with negligible part variation (dimensional results), using selected capable machines. The data-driven results provided by this lean systematic method are more robust, faster to obtain and more cost effective than the traditional single machine approach.