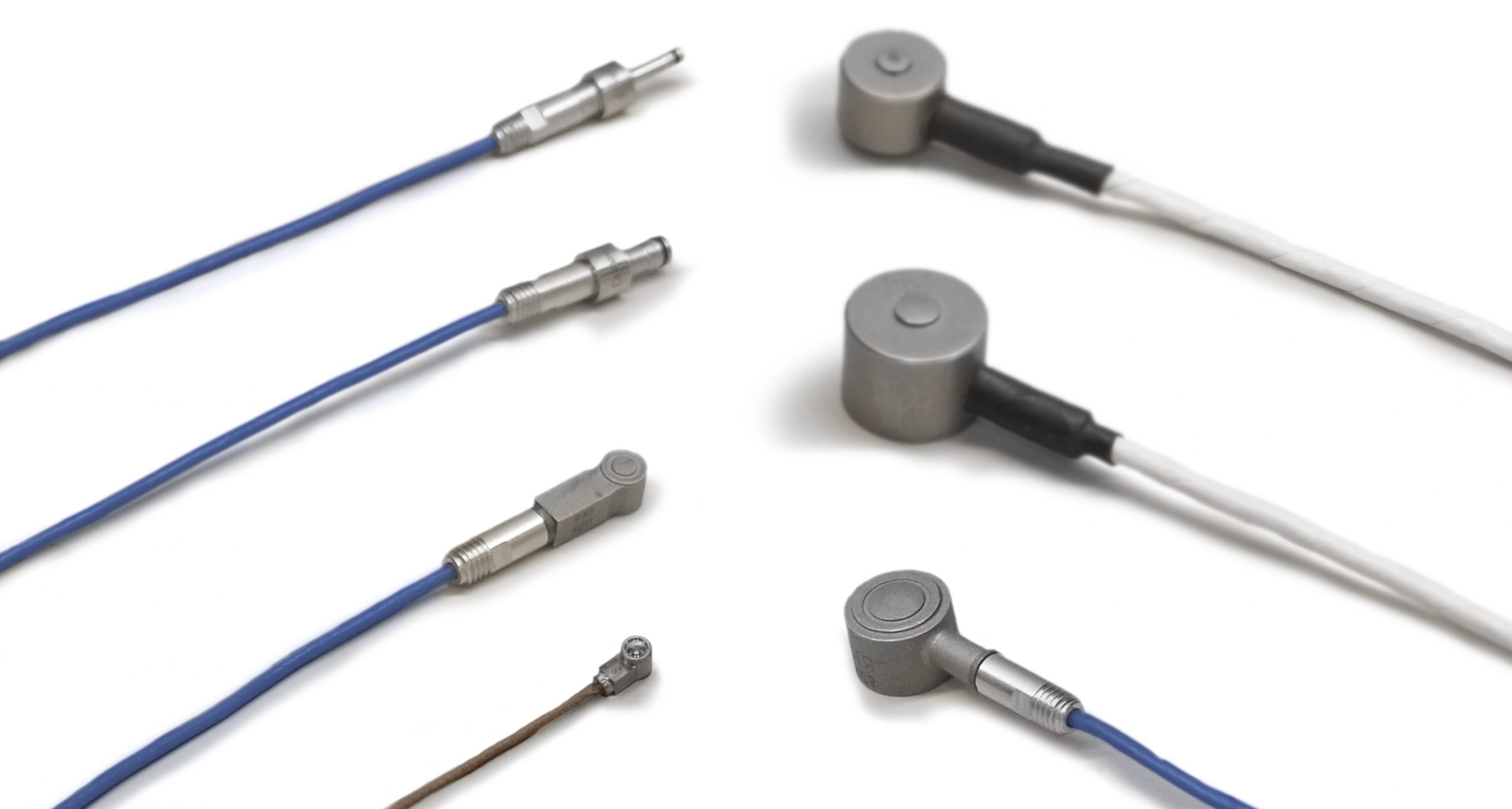
When looking at injection molding cavity pressure sensors, the sheer number of products to choose from can be a bit overwhelming. In order to choose the proper sensor for your application, it’s vital to fully understand all of the options and what will work for your specific project.
Some sensor selection considerations include:
- How the sensor will be installed
- Where it will be installed
- How much space it needs
- The temperature it needs to endure
- How many there will be in the mold
- What type of sensor technology
We’re going to focus on the type of sensor technology.
What Types of Cavity Pressure Sensors Are Used in Injection Molding?
There are two main types of sensors: strain gage and piezoelectric (piezo).
Strain gage sensors have a full or partial Wheatstone bridge strain gage sensing element (fun fact: it inspired our logo). When force is applied, the gage is deformed causing its electrical resistance to change. The resulting changes in current is interpreted by a process control system (such as CoPilot) where it can be displayed in graphical format.
Piezoelectric sensors have a quartz crystal in the sensor that, when force is applied, emits an electrical charge. This electrical charge is amplified to a signal that can then be sent to a process control system (such as CoPilot) where it can be displayed in graphical format.
Both technologies are reliable, and we recognize benefits each may have over the other depending on the application; however, we have identified strain gage sensors as our preferred technology for several reasons. Let’s review the benefits of strain gage sensors and why they are preferred in most scenarios.
What Are the Benefits of Strain Gage Sensors?
Let’s review the benefits of strain gage sensors specifically and why they might be a good option for your application.
1. Less Risk of Contamination
Contamination is any outside substance that causes inaccurate data readings. It happens when debris, water, or moisture sneaks into the electrical sections of a sensor system, greatly skewing the data.
Piezo sensor systems as a whole have many locations that can be exposed to contamination, causing drift in data and potential failure of the sensor itself. An example of this is any connection point, either at the sensor or on the side of the mold.
Strain gage sensors are highly robust and are inherently immune to all but the most severe forms of contamination. This means you can rest assured that your hardware is collecting accurate data.
2. Higher Temperature Tolerances
It’s important to take into consideration how hot you will be running your mold. Each sensor head has a maximum temperature that it can withstand—going above that will cause damage to your sensor and inaccurate data. Piezo sensors can withstand up to 392°F (200°C), whereas some strain gage sensors can withstand up to 425°F. That means they can be used in a wider array of machines and applications without risk of damage to the sensor head.
3. Better Shielding from Signal Noise
Strain gage cables are permanently mated to the sensor head, providing more shielding against ambient electrical currents or build up through the tool. Each connection point for the Piezoelectric sensors is a break in the shielding, which may allow stray electricity to interfere with the picocoulombs of signal generated by the piezoelectric crystals under load. This signal interference is then magnified by the signal amplifiers necessary to boost the crystals’ generated current to a level detectable by modern computers (such as process control systems).
4. In-Mold Sensor Diagnostics
A frequently overlooked benefit of strain gage sensors is the ability to diagnose the health of the sensor while it is installed in the mold. The readings from a strain gage sensor at rest can determine whether a cable has been crushed during installation, the sensor is improperly installed, or the sensor has been overloaded or damaged. On the other hand, piezo sensors only provide very limited data for diagnosing sensor problems. This can be helpful in detecting problems in the tool room before the mold is installed in the press, saving significant downtime if a problem occurs.
5. Lower Cost Solution
One of the biggest things that sets strain gage sensors apart from piezo is that they are a lower cost option with the same data quality as a piezo sensor. When looking at equipping all of your molds with multiple sensors per mold, the savings add up fast. Though this is important, we want to make sure that you’re receiving the proper equipment for your application based on all factors, not just cost. But if those align, this is a huge benefit and win for your budget.
Conclusion
Overall, strain gage and piezo sensors are very comparable in performance and final data displayed on a process control system. Their resolution and accuracy are in line with one another, and they both offer a large array of sensor head sizes. Strain gage sensors offer a more robust design that is more likely to provide accurate data, ease of debugging, higher temperature threshold options, and a lower cost solution with comparable results.
Want to learn if strain gage sensors are right for you? We’d be happy to help! Contact our team today.