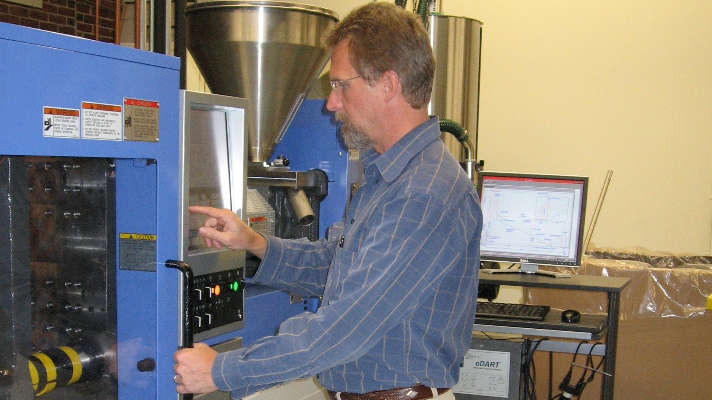
The Challenge
In 2001 we were facing numerous challenges including: thinner parts, tougher plastics, growth in regions of the world not known for plastics engineering, and producing the same parts in multiple sites around the world. It was that year that I was first introduced to RJG and their DECOUPLED MOLDING® processing techniques at an Executive Overview held at Nypro. After the Executive Overview, I was assigned to lead Nypro Clinton’s training implementation team. The goal of the team was to implement a standardized, simplified, scientific approach to injection molding, in order to improve cycle time and part quality.
The Solution
I was one of three people selected to become Master Molder® III certified in order to train Nypro employees. After my certification, we began teaching classes in July 2003. During this initial phase we learned that we needed to drive the implementation through the program managers, rather than the molding technicians or production management. They were able to drive the effective use of these methods from the planning and tryout phase and transfer them into production. The program grew towards a global scale and in August 2006 we opened the Nypro University Learning Center with four machines dedicated strictly to training. RJG’s Training provided a way for our fast growing global company to build multi-functional teams within the individual plants who can properly build a valid DECOUPLED process that:
1. Exposes issues instead of covering them, so they can be fixed before production begins.
2. Reduces the effects of normal variation in plastic and equipment for more stable products.
3. Provides evidence of abnormal variation
4. Provides a machine independent process results record so that it can be duplicated on any capable machine as the scale or location of the programs change.
5. Allows for remote support to reduce time to market, since we are all doing “it” the same way.
The Result
These teams experience RJG’s training first hand and demonstrate their skill and capability at the end of a very intense two week course, which can only be passed with a significant amount of their own time and extreme diligence. Plants are sending some of their key people out for 2 weeks, which means they have to provide coverage, plus travel and expenses and the cost of the course. A lot of time and effort has to be made to take these classes, yet people keep coming. That is one measure of the effectiveness of this training. Trainees have come from as far away as Asia and Europe and include non-Nypro employees as well as our customers.
DECOUPLED II molding has become our global standard. The RJG eDART® System with Lynx sensors is our standard for those times when DECOUPLED II is not good enough, as judged in advance by risk assessment, or after the fact due to capability issues. Many of our medical and electronics customers are very interested in building this technology in to their new molds. During training the benefits of the valid DECOUPLED III process is vividly revealed when they watch their own experiment and observe the incredible amount of control it provides when we change materials on the fly, and the parts barely change at all.
Doug Thorpe
Director, Advanced Technology
Center and Process Training
Nypro Inc.
About Nypro
Nypro is one of the largest custom injection molding and contract manufacturers in the world. We operate over 50 separate businesses in 17 countries and provide our services to the world’s largest Electronics/Telecommunications, Consumer/Industrial, Packaging, Healthcare, and Automotive companies as well as Contract Manufacturers.