See what’s happening inside the mold to improve part consistency and quality
Gathering information from inside the cavity, at the heart of the process, gives you the information needed to assure quality on every shot.
Request a Consultation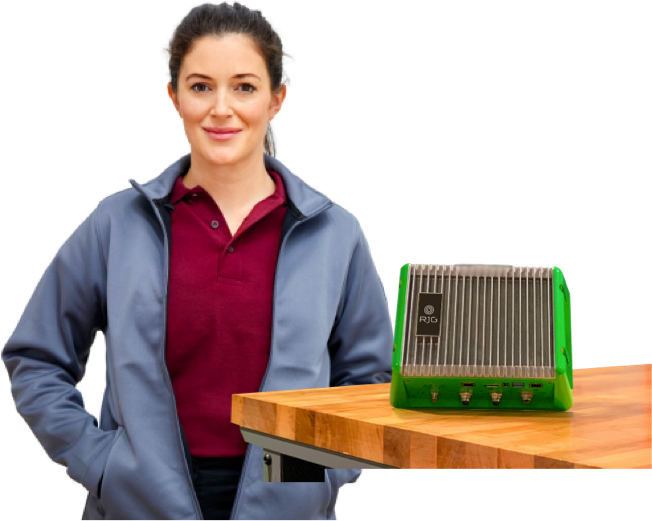
Harness the power of knowledge with injection molding sensor technology
Cavity pressure is the process variable that correlates most directly with part quality, because it’s measured where the part is made.
- Know when a process has shifted and how to adjust it back using in-cavity data
- Reduce time required to make good parts
- Track variation to eliminate guesswork while troubleshooting
- Reduce validation costs by validating processes independently of the machine
- Archive and export critical data
- Build an audit trail to reduce risk for each part shipped
- Know immediately when something changes in your process
- Automatically sort abnormal shots and eliminate manual inspections
- Stop shipping bad parts to your customers
- Precisely and consistently control the molding process
- Reduce scrap and improve part quality
- Extend the life of the tool and reduce equipment damage
Types of injection molding sensing technologies
Cavity Pressure Sensors
Cavity pressure sensors allow you to build a process around what is actually happening inside the mold. Pressure data can also help identify common molding problems, such as shorts, dimensions, sinks, flash, warp, and more.
Temperature Sensors
Temperature is critical to the manufacturing of many parts, especially those made with semi-crystalline materials or with tight dimensional tolerances. Changes or breaks in cycle time, clogged cooling lines, or improper cooling settings can dramatically impact thermal stability. In-cavity temperature sensors can help you diagnose problems and prevent shipping bad parts.
Mold Deflection Sensors
Mold Deflection Sensors measure how much the mold parting line opens on each cycle, helping to detect problems like properly set clamp tonnage, flash, or even gas traps if vents are collapsed from over-clamping. They can also be used in applications where cavity pressure sensors won't fit.
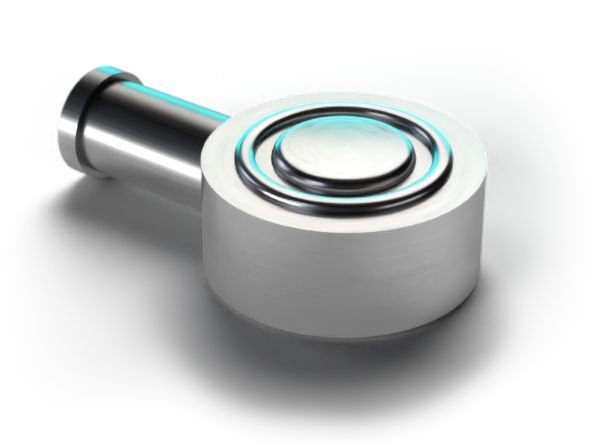
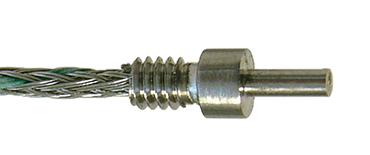
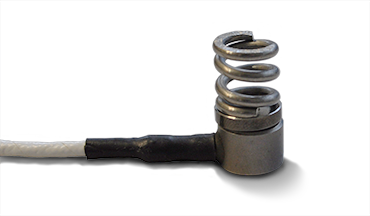
Types of cavity pressure sensor systems
Lynx® Single Channel Sensors
Our Lynx digital sensors are the most accurate and easiest to use cavity pressure sensors available today. Unique algorithms embedded in each unit significantly enhance the accuracy of these sensors. These "smart" sensors also have other key calibration information embedded to simplify the setup and daily use on the shop floor.
These sensors are ideals for applications on molds with fewer cavities where four or fewer sensors are required. Lynx single channel sensors are available with either strain gage or piezoelectric sensor technology.
Lynx Embedded Sensors
Designed for higher cavity molds, Lynx Embedded Sensors provide all the benefits of the Lynx Single Channel Sensor, but with the sensor electronics and head entirely buried in the mold, providing a single connection point on the side of the mold and eliminating outside cabling.
Benefits of Lynx embedded sensors:
- Reduced damage during use and tool maintenance
- Reduced footprint and cabling on the side of the mold
- Well-suited for medium to high (4-31) cavity pressure sensor applications
Multi-Channel Strain Gage System
This low-profile, robust hardware system simplifies in-mold installations for molds with four or more button style sensors and saves real estate on the mold. It allows you to connect up to eight strain gage sensors to one connection point on the mold, reducing the footprint of hardware and saving costs. Mold-ID identifies the sensors and the mold to the CoPilot and eDART systems, so you can be sure you have the right mold running and the correct sensors selected.
Benefits of multi-channel strain gage sensors and Mold ID:
- Reduced footprint on multi-cavity molds
- Low profile and robust
- Saves costs over other multi-cavity solutions
- Simplified installation
Multi-Channel Piezo System
The multi-channel piezo cavity pressure system allows injection molders to connect up to eight piezoelectric sensors to one connection point in the mold. The interface with Mold-ID identifies the sensors and the mold to the CoPilot and eDART systems, so you can be sure you have the right mold running and the correct sensors selected.
Benefits of multi-channel piezo sensors:
- Reduced footprint on multi-cavity molds
- Low profile and robust
- Simplified installation
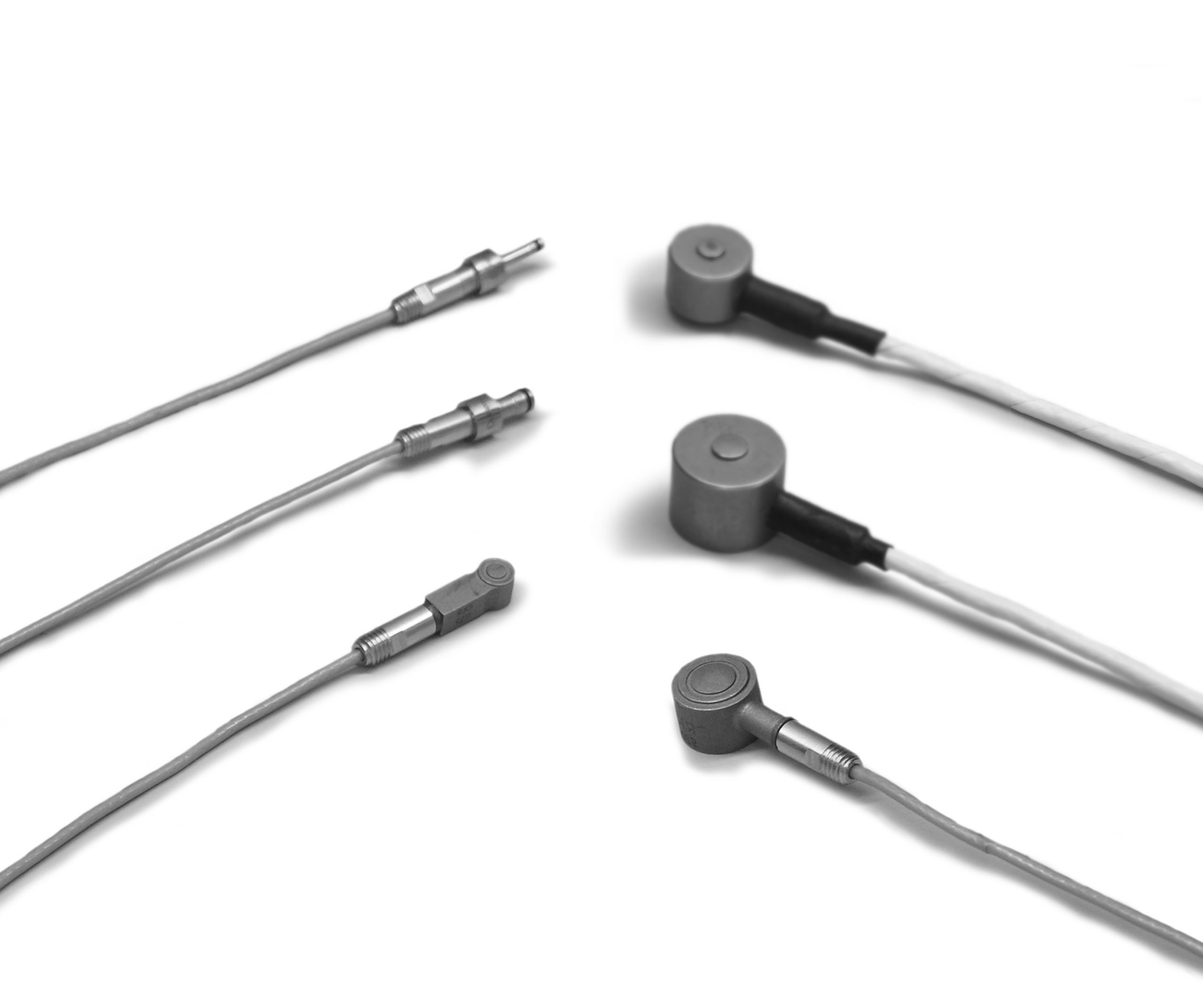
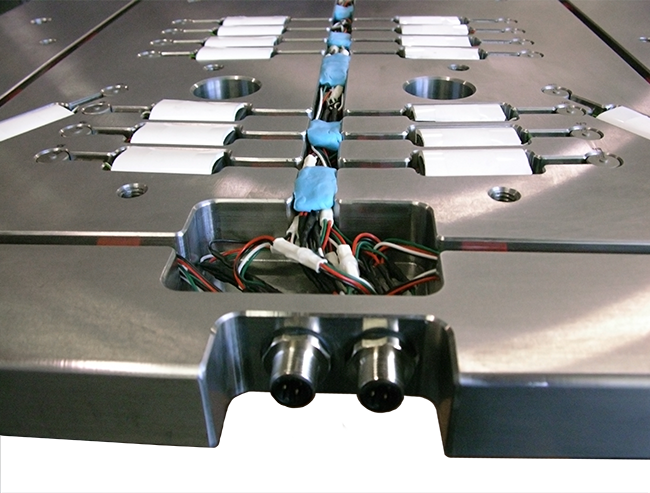
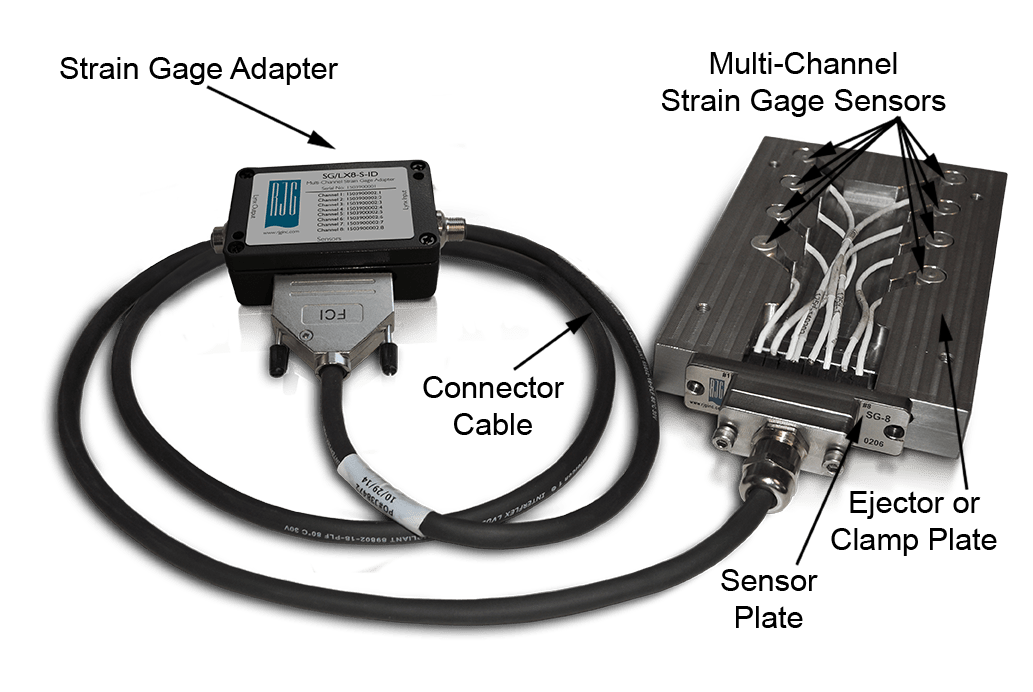
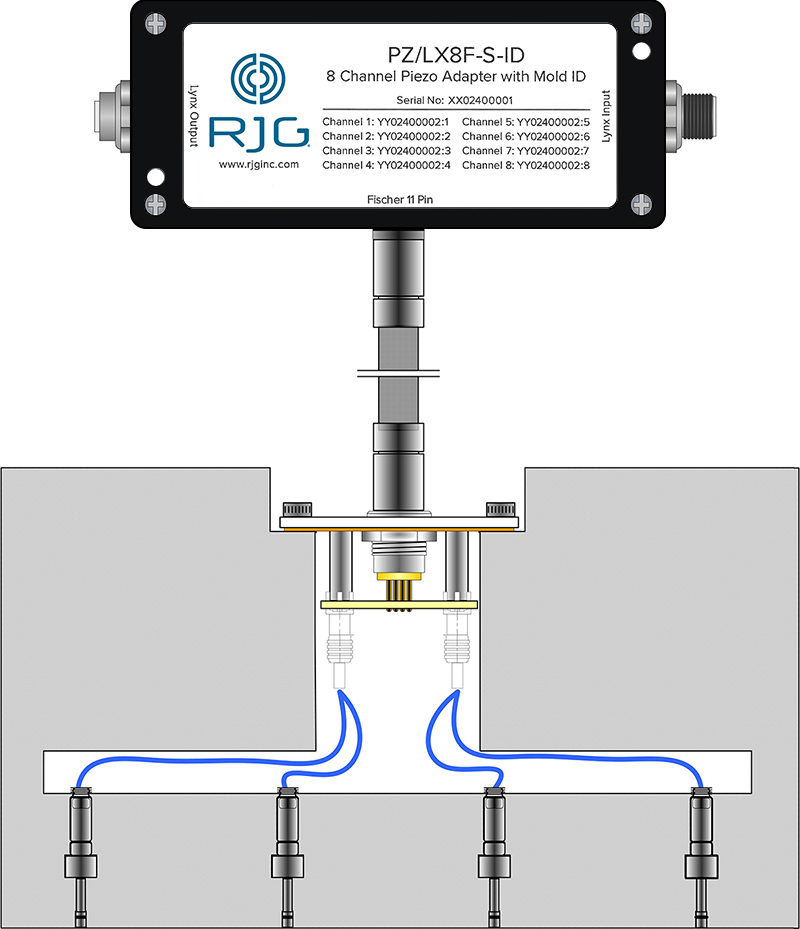
We're here to ensure your sensors are working hard for you
Sensor Selection
Choosing the right sensor is the key to successful instrumentation. We will provide personalized sensor recommendations, so you get the accurate information you need upfront.
Implementation Strategies
Sensor placement and installation techniques can greatly affect the accuracy and efficiency of your outcomes. We will ensure they're collecting the vital data for your process.
Sensor Testers
Poorly installed or damaged sensors can lead to bad parts getting out the door and costly machine downtime. Sensor testers allow you to ensure sensors are working properly and accurately before the tool goes into the press.
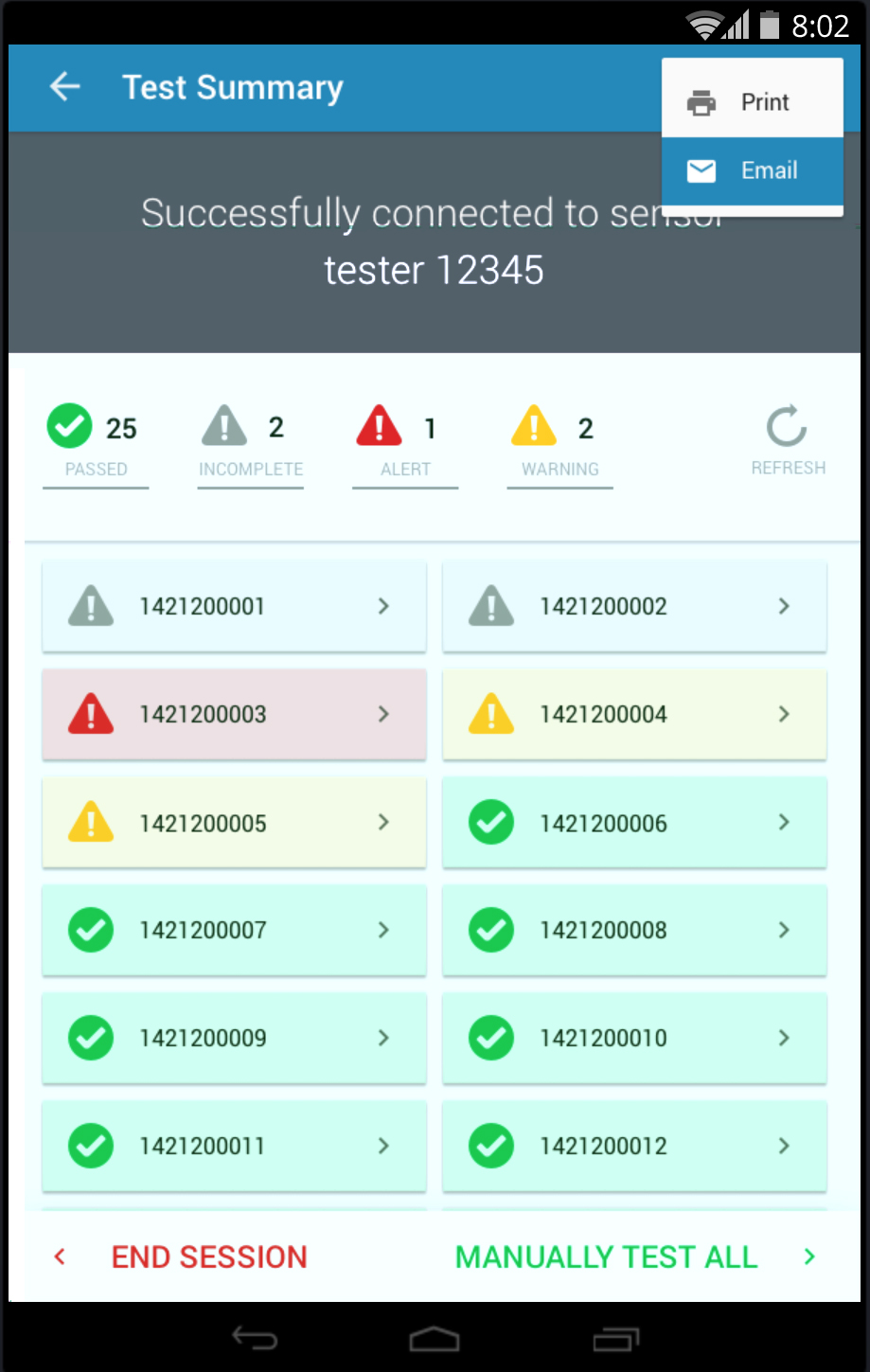
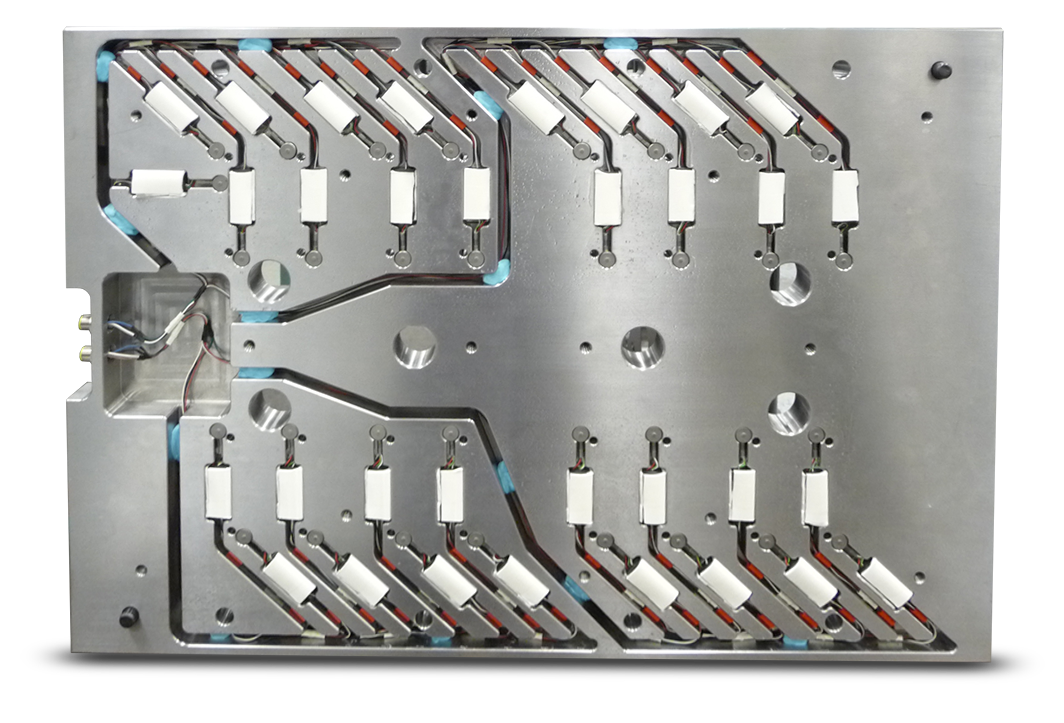
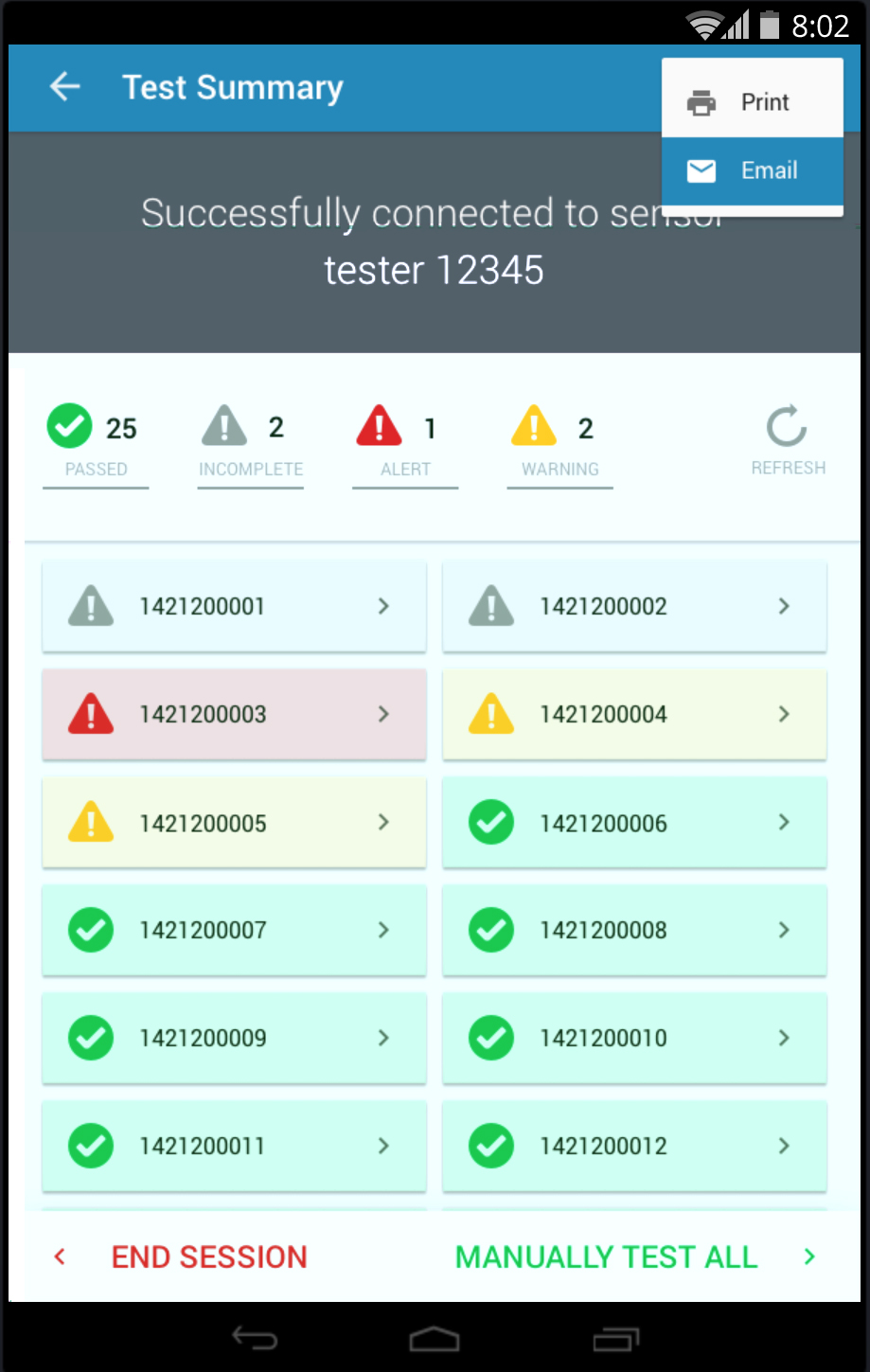
Testimonials
Hear what our amazing customers have to say about in-mold sensors:
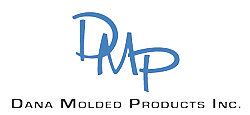
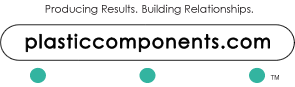
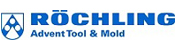
Validating Medical Molded Parts with Confidence
“Our customers have a clear understanding of what RJG allows us to see, understand, and document, which clearly provides them with a higher level of confidence that their product is the best it can be.,.”
Fred Chamberlain
VP Operations Dana Molded Products
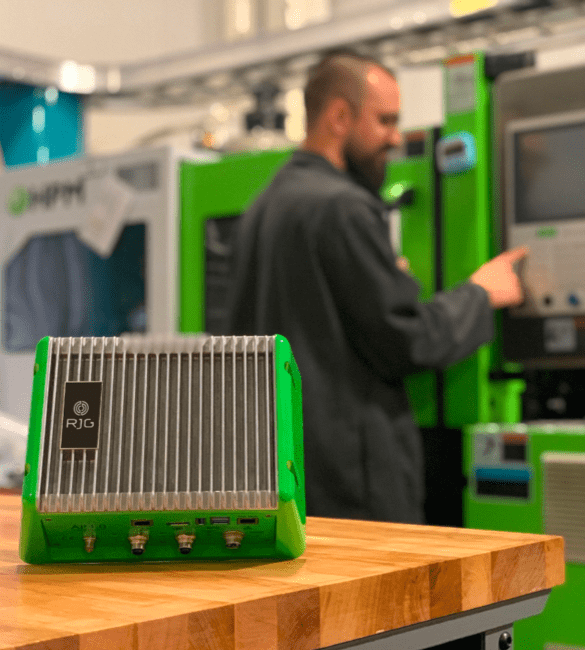
Like Having a Full-Time Auditor at Each Press
““RJG has provided us with both quality gains and cost savings. In using the software, we are able to lower the frequency of quality checks needed to ensure good parts. Using the eDART System and in-mold sensors is like having a full-time auditor at each press.,.”
Chris Laverty
Manufacturing Engineer Plastic Components, Inc.
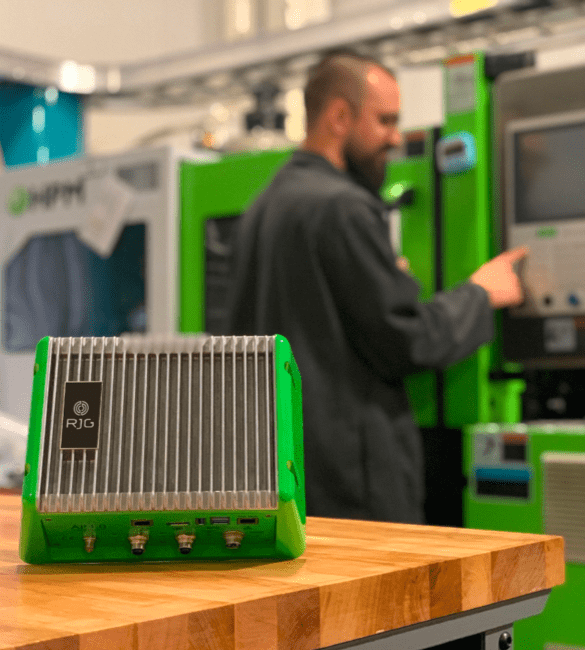
Quality Again and Again and Again
“Advent designed & constructed 16 cavity mold incorporating a cavity pressure sensor in each cavity... Since Advent started production of this part over 5 years and 250 million parts ago, we have not shipped a defective part to the customer..,.”
Ken Desrosiers
President Advent Tool and Mold Co.
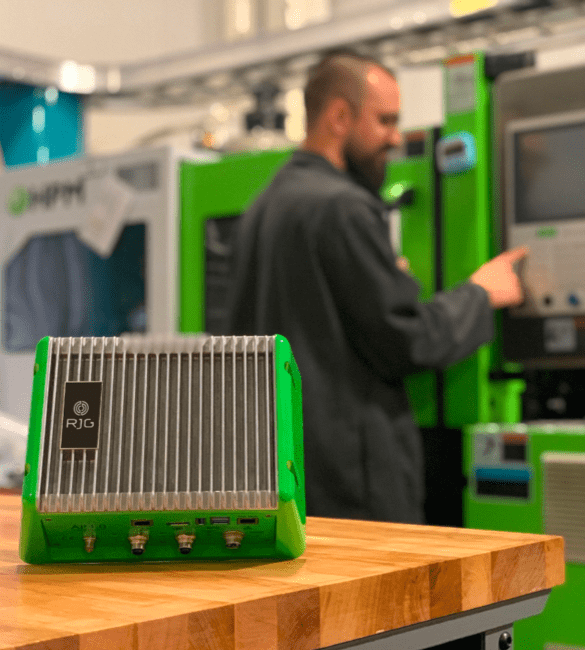
Sensor resources
View more information on these products
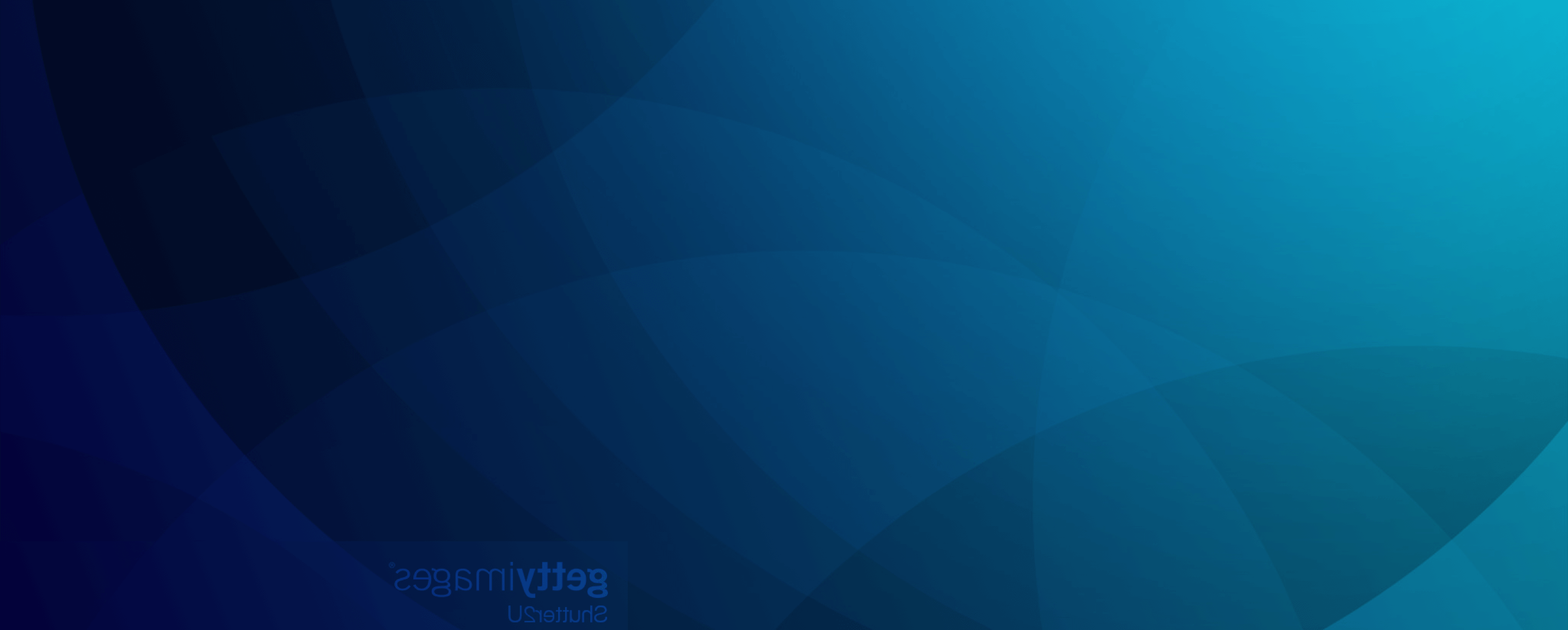