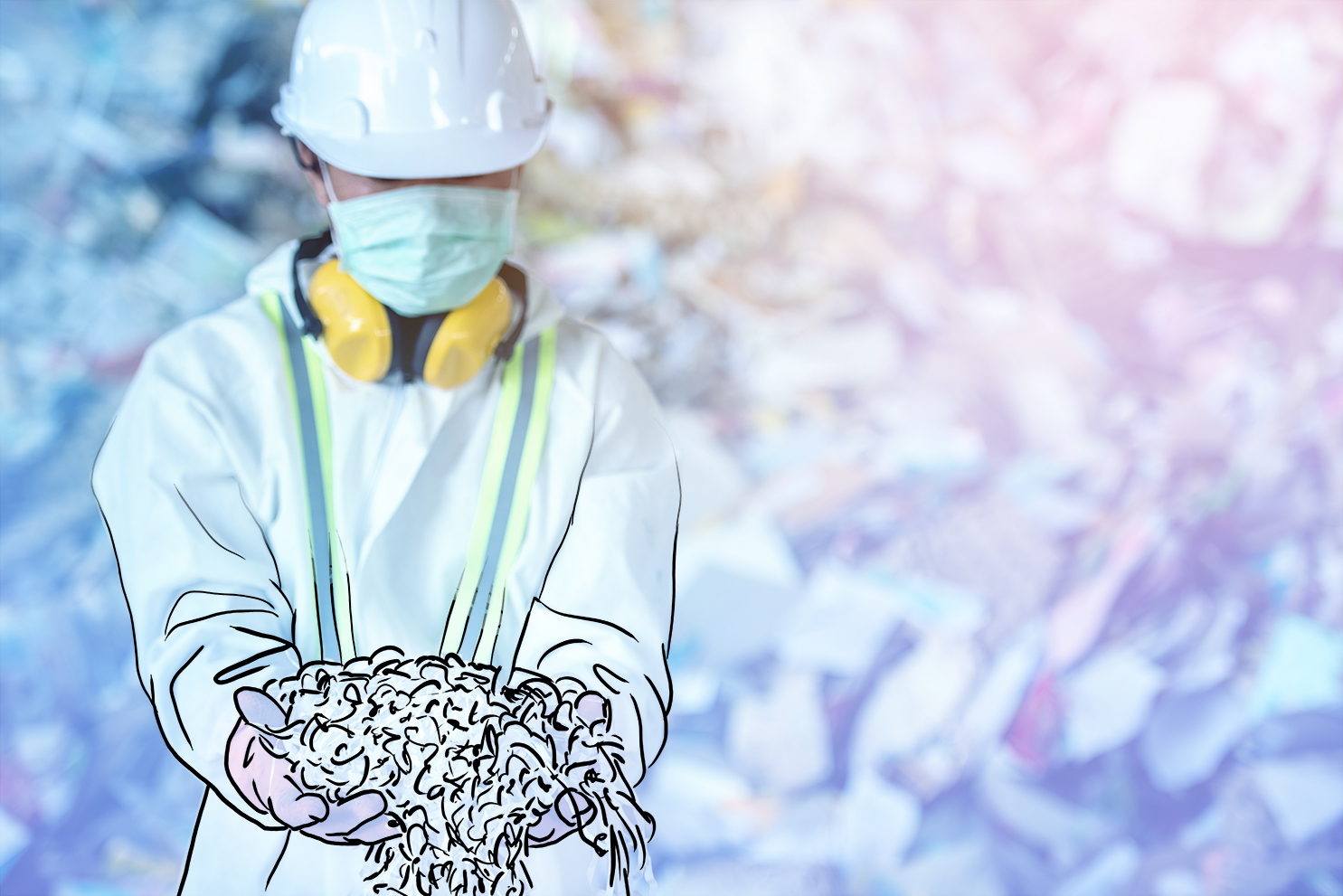
When you think of reducing waste, scrap comes to mind, right? Obviously that’s a huge part of it, but… only a part of it. Waste exists in all areas of processes, from scrap to machine downtime to time spent fixing processes, and everything in between. By minimizing waste, you can enhance operational efficiency, reduce costs, and contribute to environmental sustainability. In this article, we will explore effective strategies to help you reduce all types of waste in your injection molding business and achieve long-term success.
Optimize Material Usage
Material waste is a significant concern in injection molding. To minimize it, start by accurately calculating the required material quantities for each production run. Utilize scientific molding techniques to optimize the molding process, achieving high-quality parts with minimal material consumption. Implement regrind programs to recycle excess material and reduce the need for fresh resin. Consider using recycled or bio-based materials, where feasible, to reduce environmental impact further.
Implement Lean Manufacturing Principles
Adopting lean manufacturing principles can significantly reduce waste throughout your operations. Streamline your production workflow to eliminate non-value-added activities, reduce wait times, and optimize material flow. Implement just-in-time (JIT) inventory systems to minimize excess stock and reduce carrying costs. Emphasize continuous improvement, empowering employees to identify and eliminate waste in their work areas.
Conduct Waste Audits
Regular waste audits can help you identify specific areas where waste occurs and develop targeted solutions. Analyze your processes, machinery, and material handling practices to identify inefficiencies and waste generation points. Measure and track waste metrics such as scrap rates, rejected parts, and excess material usage utilizing The Hub®. This data will provide insights into the root causes of waste and guide your improvement efforts.
Optimize Production Planning
Efficient production planning is crucial for waste reduction. Implement demand forecasting techniques to anticipate customer requirements accurately and optimize production schedules. Utilize software tools to align production orders, minimize changeovers, and reduce machine idle time. Effective planning ensures optimal machine utilization, reduces energy consumption, and minimizes waste associated with inefficient production setups.
Implement Effective Quality Control Measures
Poor quality control leads to increased waste and rework. Implement robust quality control measures to detect and prevent defects early in the production process (starting with part and mold design). Utilize statistical process control technology such as CoPilot® to monitor and maintain consistent part quality, reduce scrap, and lower machine downtime. Train employees on quality standards, conduct regular inspections, and provide feedback loops to address issues promptly. By ensuring high-quality production, you can minimize waste associated with rejected or reworked parts.
Employee Training and Engagement
Engage and educate your employees on waste reduction strategies. Provide comprehensive training on injection molding techniques, quality control practices, and lean manufacturing principles. Trained employees are much less likely to produce excess scrap. Their ability to effectively fix processes will reduce machine downtime, scrap, and the need to bog down engineers’ valuable time. Foster a culture of responsibility and environmental awareness, encouraging employees to contribute ideas for waste reduction and process improvement.
Conclusion
Waste reduction is an ongoing process that requires a commitment to continuous improvement. Encourage employees to share suggestions and ideas for waste reduction regularly. Implement regular review meetings or Kaizen events to identify improvement opportunities and implement sustainable solutions. Celebrate successes and recognize employees’ contributions to improving operational efficiency.
By implementing these strategies, you can achieve sustainable success by reducing waste, increasing efficiency, and making a positive impact on the environment.
Next Steps
Sound a bit overwhelming? Let us help! Our new RJG SMART MethodSM will provide an in-depth analysis of the health of your organization, pinpoint areas of improvement, and create a custom plan to improve your profitability. Then we will help with implementation and ensuring your entire team is onboard.