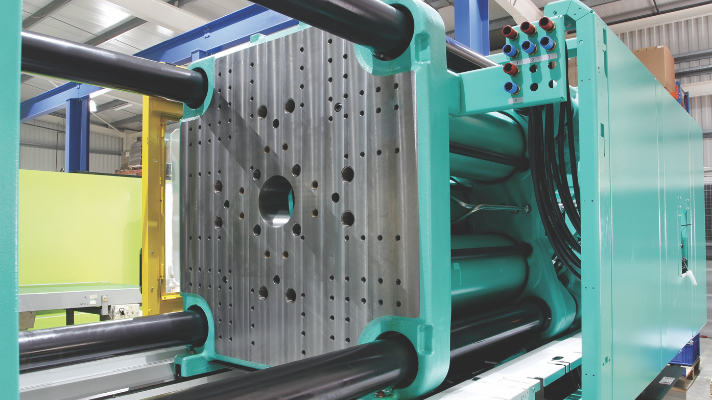
a cura di Jim Clifford, consulente/formatore presso RJG La forza di chiusura è uno dei parametri più sottovalutati del processo di stampaggio a iniezione. Ho perso il conto delle volte in cui mi sono recato vicino a una macchina per lo stampaggio per verificare se la forza di chiusura era impostata al massimo. Questo può infatti causare danni alla macchina o allo stampo se quest’ultimo non è correttamente dimensionato per la macchina in cui è in lavorazione. Allora, cos’è la forza di chiusura? Che importanza ha? E come si calcola?
Cos’è la forza di chiusura?
La forza di chiusura disponibile è il tonnellaggio di chiusura di cui la macchina è capace. La macchina deve avere una forza di chiusura sufficiente a mantenere chiuso lo stampo per contrastare la pressione della plastica che si svilupperà all’interno della cavità dello stampo e del canale freddo. Generalmente si consiglia di calcolare la forza di chiusura necessaria per ogni singola parte, piuttosto che impostarla sulla macchina al valore massimo.Perché la forza di chiusura è importante?
Quante sono i pezzi lavorati nel vostro impianto in cui ogni dimensione critica è al valore medio o al centro della tolleranza? In un mondo perfetto, la risposta sarebbe tutti, ma, come ben sappiamo, non siamo in un mondo perfetto. Nella maggioranza dei casi ci sono alcune dimensioni critiche che sono in tolleranza, ma vicine al limite inferiore o superiore. Se la forza di chiusura viene regolata senza essere ottimizzata, si può correre il rischio di portare alcune dimensioni fuori dalle specifiche. La situazione può diventare ancora più difficile se è già stata richiesta una deviazione al vostro cliente. Cosa succederebbe se doveste comunicare al vostro cliente che avete bisogno di una deviazione per una tolleranza ancora più ampia su una dimensione critica? Poi, alla lavorazione successiva, si avvia la macchina con il tonnellaggio di chiusura impostato originalmente, ma ora la dimensione è cambiata. E questo potrebbe mettervi di nuovo in una posizione scomoda. Ecco di seguito un esempio che mostra quanto sia importante la forza di chiusura. Di recente, nel nostro laboratorio, ho analizzato un campione modificando solo un setpoint singolare. Come si può vedere nella Fig. 1 qui sotto, questa impostazione ha modificato il volume massimo di iniezione, la pressione massima nella cavità, la velocità di pressurizzazione e la velocità di raffreddamento. Ha influenzato la lunghezza, la larghezza e lo spessore dei pezzi. Quale variabile avrei potuto modificare in modo da compromettere il processo? Bisognerebbe osservare la situazione dal punto di vista della plastica utilizzando le quattro variabili specifiche: calore, flusso, pressione e raffreddamento. Quale di queste variabili avrebbe più effetto sulle dimensioni del pezzo? Risposta: il tonnellaggio di chiusura. Lo so… è una domanda a trabocchetto, ma si tratta di un parametro così importante che è stato persino considerato come la quinta variabile. Alla maggior parte delle persone non verrebbe in mente questa regolazione perché non ha nessun effetto sulle dimensioni dei pezzi, ma può cambiare totalmente quello che accade all’interno della cavità. Troppo spesso si effettuano altre regolazioni del processo per riportare le dimensioni in tolleranza, senza mai considerare la forza di chiusura.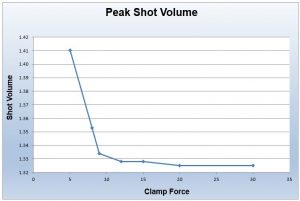
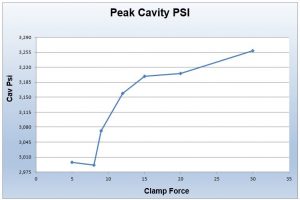
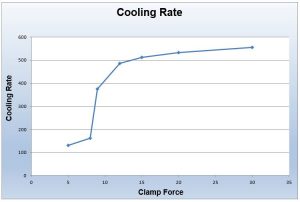
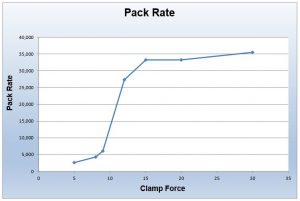
Come si calcola la forza di chiusura?
Per prima cosa, bisogna calcolare l’area totale proiettata del pezzo. Si tratta dell’area bidimensionale proiettata di tutti i pezzi e dei canali freddi sulla linea di divisione dello stampo. Vi chiederete: perché calcolare l’area del canale se il vostro obiettivo è quello di ottenere pezzi buoni e non di avere canali freddi buoni? Bisogna tenere conto del fatto che i canali freddi sono soggetti alla pressione della plastica che cerca di forzare l’apertura delle due semi sezioni dello stampo. Una volta calcolata l’area bidimensionale proiettata di tutti i pezzi e dei canali freddi, essa va moltiplicata per la forza di chiusura raccomandata dal fornitore del materiale che, generalmente, indica questo parametro in tonnellate per pollice al quadrato (vedere calcolo nella Fig. 2 qui sotto). Questo calcolo fornisce indicativamente la quantità di forza di chiusura necessaria, potrebbe tuttavia non essere esatto. Quando i fornitori del materiale stabiliscono il requisito della forza di chiusura, non lo fanno sul vostro stampo preciso. Se si desidera ottenere un valore più preciso della forza di chiusura raccomandata per il proprio pezzo specifico, è possibile utilizzare la pressione media in cavità se lo stampo è dotato di sensori della pressione in cavità. Per esempio, usiamo uno stampo che ha una pressione dopo il punto di iniezione di 9000 ppsi e una pressione a fine cavità di 3000 ppsi. Quando sommiamo entrambe queste pressioni e poi le dividiamo per due, si ottiene una pressione media di cavità di 6000 ppsi. Dal momento che valutiamo le forze di chiusura per lo stampaggio a iniezione in tonnellate, dovremo dividere 6000 ppsi per 2000 libbre, pari a 3 tonnellate per pollice al quadrato. Ora è possibile utilizzare questa forza di chiusura moltiplicandola per l’area totale proiettata in modo da ottenere la forza di chiusura raccomandata per questo stampo. Questa formula è riportata anche nella Fig. 2 qui sotto.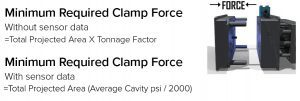
Ottimizzazione per peso del pezzo
Un altro metodo per ottimizzare il tonnellaggio di chiusura prevede la regolazione dei parametri e l’osservazione del peso del pezzo. Iniziare a lavorare i pezzi riempiti e compattati a un livello accettabile con un tonnellaggio di chiusura più alto, poi ridurre il tonnellaggio di chiusura e prendere nota del peso del pezzo. Quando si nota che il peso del pezzo inizia ad aumentare, è il punto in cui le due semi sezioni dello stampo iniziano a separarsi. Il grafico sottostante in Fig. 3 mostra l’esempio di un campione che ho eseguito con uno stampo nel nostro laboratorio. Si può vedere che da 12 tonnellate fino a 30 tonnellate il peso del pezzo è rimasto abbastanza allineato. Impostando il tonnellaggio di chiusura a 10 tonnellate o meno, il peso del pezzo ha iniziato ad aumentare. In una situazione di questo tipo, stabilirei il tonnellaggio di chiusura a 15 tonnellate, in modo avere una garanzia di sicurezza. Se fossimo passati al tonnellaggio raccomandato dal fornitore del materiale, pari a 3 tonnellate per pollice al quadrato, avremmo applicato un tonnellaggio di chiusura di 25 tonnellate. Ottimizzando la forza di chiusura in base al peso del pezzo, lo stampo ha la possibilità di sfiatare più facilmente, previene l’eccessiva chiusura e permette di risparmiare energia.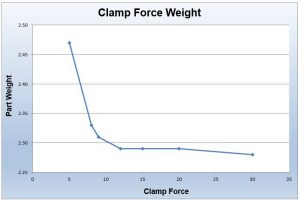
Deformazione dello stampo in base al tonnellaggio di chiusura
Lo stampo che abbiamo utilizzato per il campione era dotato di sensori di deformazione dello stampo, in modo da potere osservare in che misura lo stampo veniva deformato a ogni tonnellaggio di chiusura. Come si può vedere nella Fig. 4, la deformazione dello stampo è in diretta correlazione con l’aumento del peso del pezzo alle diverse impostazioni di tonnellaggio di chiusura. Avere sensori di deformazione nello stampo può essere molto utile per verificare se la forza di chiusura si è modificata o se sta succedendo qualcosa allo stampo stesso. Se si dispone di un eDART® con sensori di deformazione nello stampo, è possibile salvare un modello e verificare immediatamente se la deformazione dello stampo si è modificata. Questo esempio vi fa capire come sia importante tenere in considerazione anche la forza di chiusura e non solo le altre quattro variabili.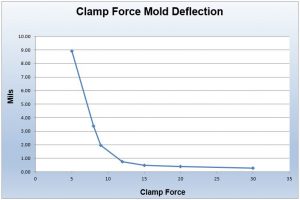
Altre misurazioni
Durante lo svolgimento della prova sul campione, ho anche deciso di effettuare le misurazioni dei pezzi con ciascuna impostazione della forza di chiusura. Il campione era un semplice rettangolo, quindi ho misurato la lunghezza, la larghezza e lo spessore. Sono rimasto sorpreso nel vedere che tutte e tre le dimensioni si sono scostate in tutte le diverse impostazioni della forza di chiusura.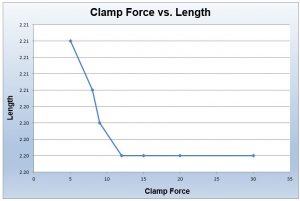
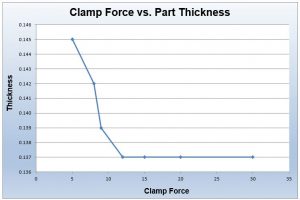
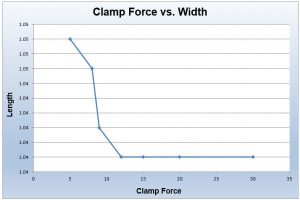