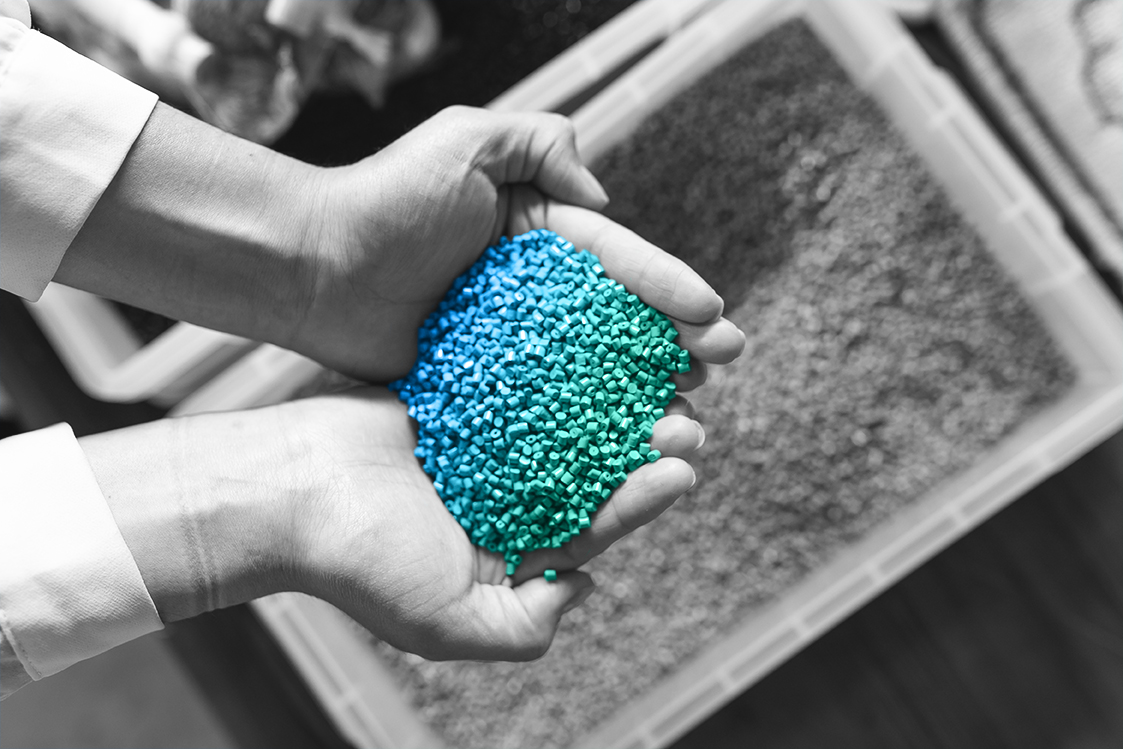
Achieving consistent quality in injection molding is heavily reliant on the proper handling of plastic resins. One critical aspect often overlooked is the moisture content in plastic resins, which can significantly impact the final product’s quality. In this blog post, we’ll delve into the importance of drying plastic resins before injection molding and explore best practices to ensure optimal results.
The Importance of Drying Plastic Resins
Plastic resins, particularly hygroscopic ones like nylon, PET, and polycarbonate, have a natural tendency to absorb moisture from the environment. This moisture content can lead to various issues during the injection molding process, including:
- Porosity: Moisture trapped within the resin can form bubbles or voids in the molded parts, resulting in defects and compromised structural integrity.
- Surface defects: Excess moisture can cause surface imperfections such as splaying, silver streaks, or delamination, detracting from the part’s appearance and functionality.
- Dimensional instability: Moisture-induced changes in the resin’s viscosity and shrinkage behavior can lead to dimensional variations in the molded parts, affecting their fit and function.
The Dangers of Over-Drying Plastic Resins
Drying a material too much can lead to degradation of the resin, especially in the case of thermoplastic polymers. The degradation occurs due to the combination of heat, time, and exposure to elevated temperatures during the drying process. Here are some ways excessive drying can degrade resin:
- Overheating: Many resins have recommended drying temperatures, and exceeding these temperatures during the drying process can cause thermal degradation. Overheating can lead to the breakdown of polymer chains, resulting in a decrease in molecular weight and, consequently, a reduction in the material’s mechanical properties.
- Extended Drying Time: Prolonged exposure to elevated temperatures during the drying process, even within recommended temperature ranges, can contribute to resin degradation. This is particularly true for materials sensitive to heat or those with lower thermal stability.
- Oxidation: Some polymers are susceptible to oxidation when exposed to air at high temperatures. Oxygen in the air can react with the polymer chains, leading to chain scission and the formation of by-products that may affect the material’s properties.
- Color Change: Excessive drying can result in discoloration of the resin. This discoloration is often a sign of thermal degradation, and the change in color may indicate changes in the chemical structure of the polymer.
- Formation of Gels: In some cases, over-drying can cause the formation of gels or agglomerates within the resin. These gels can lead to processing difficulties and negatively impact the final product’s appearance and performance.
Best Practices for Drying Plastic Resin
There is not one standard for all resins—it’s important to review each material’s data sheet to determine optimal drying time and temperature. If you don’t have access to the data sheet, there are some tests that can be done to help determine this data as well. Here are some best practices for drying plastic resin.
- Preconditioning:
– Store resin in a climate-controlled environment with low humidity levels to minimize moisture absorption.
– If resin has been exposed to ambient conditions for an extended period, pre-dry it to remove absorbed moisture before injection molding. - Moisture Analysis:
– Conduct regular moisture content analysis using moisture meters or Karl Fischer titration (explained below) to quantify the amount of moisture present in the resin accurately.
– Establish moisture content acceptance criteria based on resin type, grade, and processing requirements. - Proper Drying Equipment:
– Invest in high-quality drying equipment specifically designed for plastic resins, such as desiccant or compressed air dryers.
– Ensure the drying equipment’s temperature, airflow, and dew point settings are optimized for the resin being processed. - Drying Parameters:
– Follow resin manufacturer recommendations for drying temperatures and times to prevent thermal degradation while effectively removing moisture.
– Avoid excessive drying temperatures or prolonged exposure, as they can degrade resin properties and compromise part quality. - Handling and Storage:
– Use sealed containers or moisture-proof packaging to protect resin from exposure to ambient moisture during storage and transportation.
– Minimize material handling time to reduce the risk of moisture reabsorption before injection molding. - Process Monitoring:
– Implement monitoring and control systems (like CoPilot) to track drying parameters, including temperature, airflow, and dew point, to ensure consistency and repeatability.
– Regularly inspect dried resin for visual signs of moisture-related defects and adjust drying parameters as needed.
The Karl Fischer Titration Process
Karl Fischer titration is a method used to measure the amount of water (moisture) in a sample. Imagine you have a sponge, and you want to know exactly how much water it’s holding. Karl Fischer titration is like squeezing that sponge and measuring the amount of water that comes out.
Here’s how it works:
- First, you take a small sample of the material you want to test, which could be anything from a liquid to a solid.
- Then, you mix that sample with a special solution called the Karl Fischer reagent. This reagent reacts with water but not with other substances in the sample.
- As the reaction happens, the amount of reagent used up tells us how much water was in the sample. It’s like counting how many drops of water the sponge released when you squeezed it.
- By measuring the amount of Karl Fischer reagent used, we can calculate the exact moisture content of the sample.
Conclusion
Properly drying plastic resins before injection molding is essential for achieving high-quality, defect-free parts. By understanding the impact of moisture on resin properties and implementing best practices for drying, manufacturers can optimize their injection molding processes, reduce scrap rates, and enhance product performance and consistency. With meticulous attention to detail and adherence to recommended guidelines, mastering resin drying can significantly contribute to overall manufacturing success in the injection molding industry.