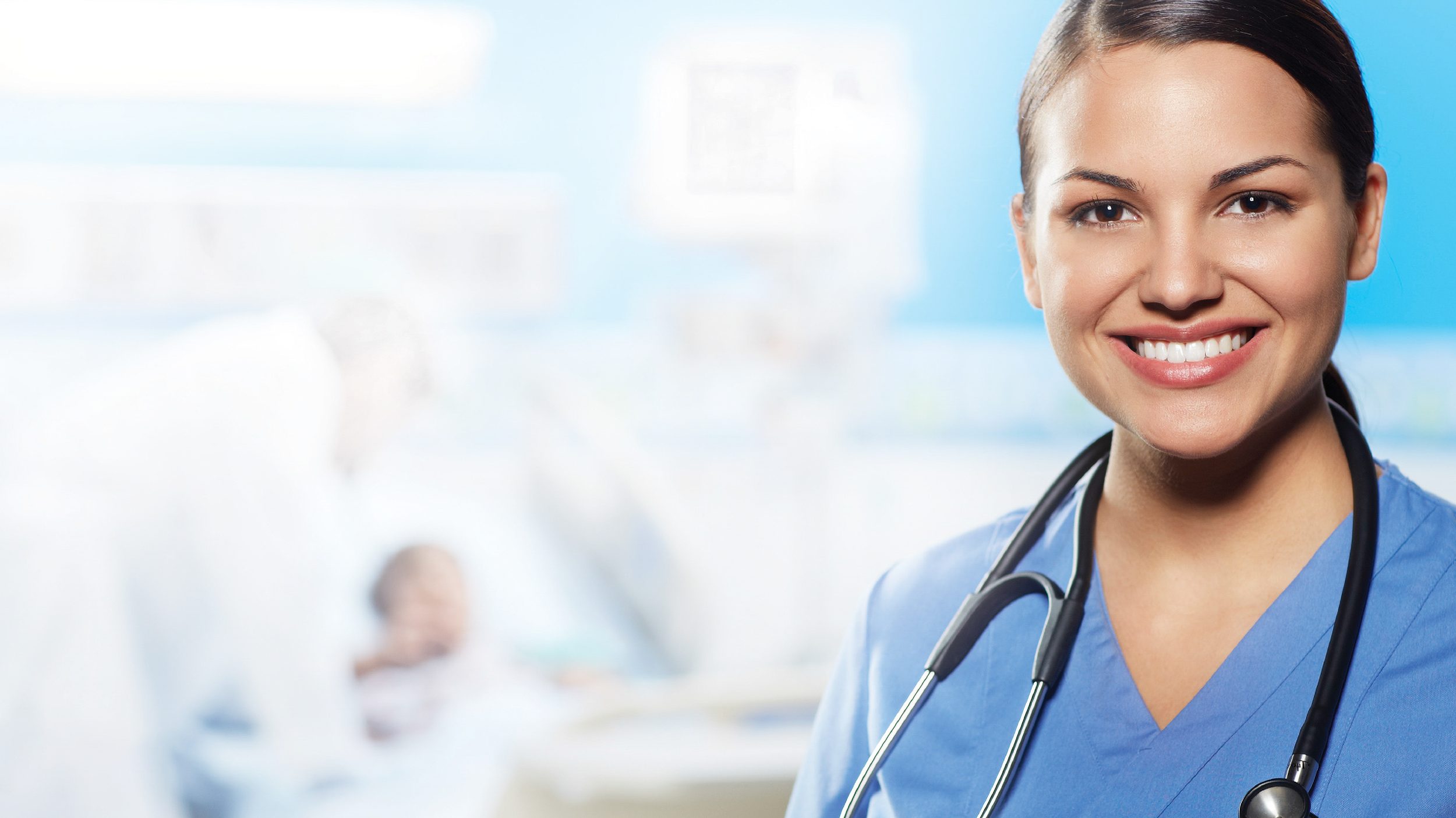
The Challenge
Many of the parts engineered at ICU Medical require extremely specific and precise molding processes, however ours revealed subtle inconsistencies that often resulted in questionable or scrap parts. We decided we needed to improve, maintain, and troubleshoot our molding process in order to provide consistency among process techs and methods and easily spot when processes were drifting.
The Solution
After searching through various options for molding training and technology, we decided to reach out to RJG for help. Getting buy-in was simple, as many of our engineers and techs were already familiar with their work. We brought RJG in, studied their scientific methods, adopted their philosophy, and entered our engineers and techs into their training program in order to implement their technology.
The Result
Since looking at the molding process from the plastic’s point of view, we have significantly reduced our time spent troubleshooting. By turning a trial and error process into a step-by-step walkthrough, we’re able to immediately understand what went wrong and why. This controlled environment speeds up production time, reduces scrap, improves overall quality, and ultimately increases our profit margin.
RJG also helped us create consistency between the engineering and production teams. The built-in log and template make it exponentially easier for techs to hand their machines over at the end of the day. They’re able to know exactly when there was an anomaly, why it occurred, and how the tech resolved the issue. Having actual values for process parameters rather than set points allows us to easily see the process and whether or not it has moved, which is not a feature available when using settings.
Overall, RJG was an investment worth making, one we’d gladly do all over again, and we look forward to continue working with them in the future.
Rick Godfrey
Molding Manager
ICU Medical
About ICU Medical
ICU Medical connects patients and caregivers through safe, life-saving, life-enhancing medical devices. We provide clinicians around the world with innovative and cost-effective patient care solutions for unmet clinical needs. Because our products are relied on to improve patient outcomes by helping reduce bloodstream infections and protect healthcare workers from exposure, it is crucial that every single part we make is of the utmost quality and precision. A single imperfection could be detrimental. Our desire to redefine the limits of patient and healthcare worker safety starts with our molding process.