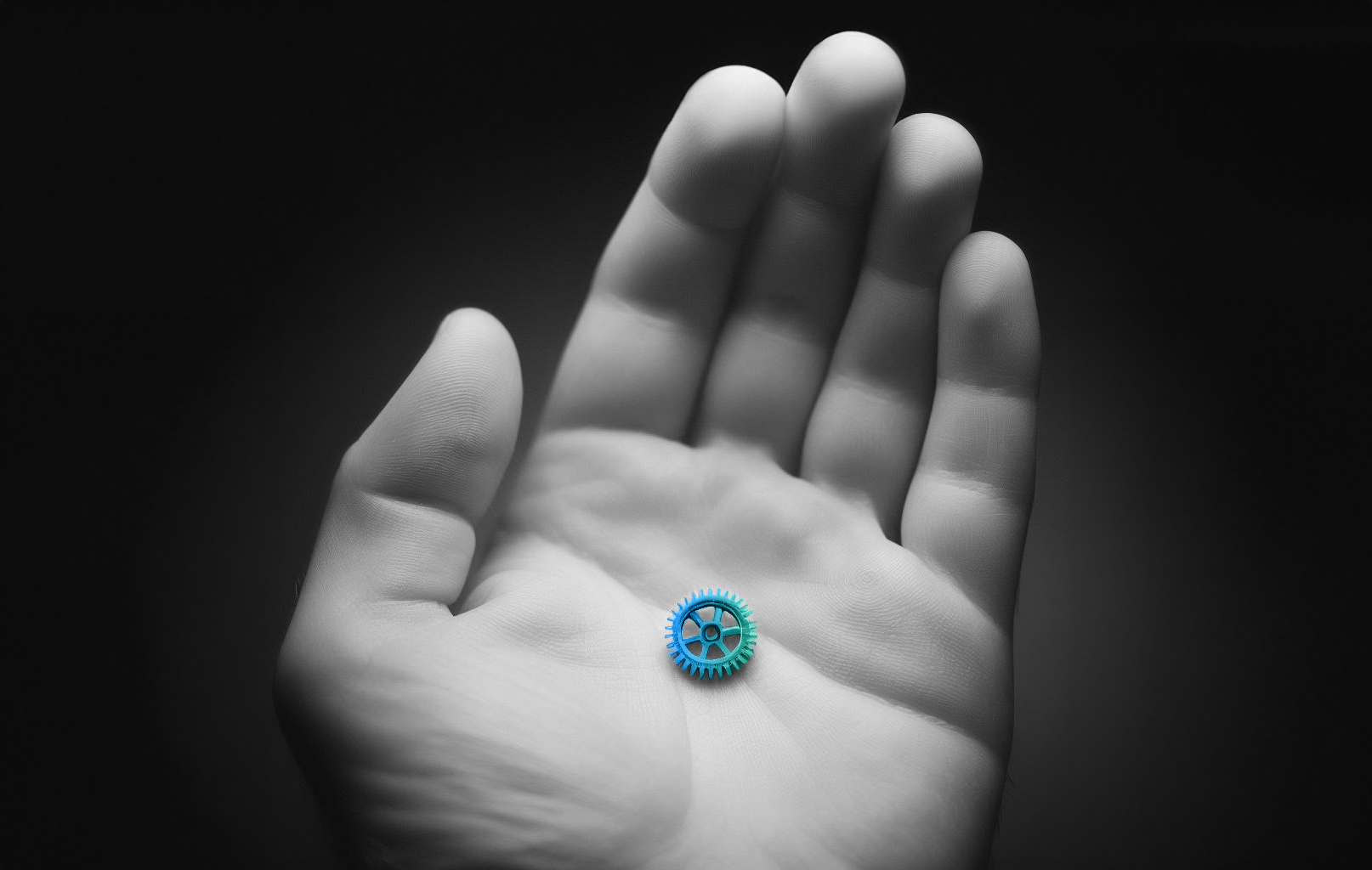
Micro-injection molding has emerged as a revolutionary manufacturing process, providing a gateway to the creation of intricate and tiny components for various industries. This technique has gained prominence due to its ability to produce precise, high-quality, and cost-effective small-scale parts. In this blog post, we will explore the advantages and challenges associated with micro-injection molding.
Advantages of Micro-Injection Molding:
1. Precision and Accuracy:
Micro-injection molding excels in producing miniature components with unparalleled precision and accuracy. The process allows for the creation of intricate details and complex geometries, meeting the stringent demands of industries such as electronics and medical devices.
2. Cost-Effectiveness:
Despite its advanced capabilities, micro-injection molding is often more cost-effective than alternative manufacturing methods for small, intricate parts. The ability to produce large quantities of precise components in a short timeframe contributes to overall cost efficiency.
3. Material Versatility:
Micro-injection molding supports a wide range of materials, including various thermoplastics and bioresorbable polymers. This versatility allows manufacturers to choose materials tailored to the specific requirements of the end product.
4. Reduced Material Waste:
The process minimizes material waste as it is designed for producing small parts with minimal excess material. This is especially advantageous in terms of cost and environmental sustainability.
5. Shorter Production Time:
Micro-injection molding is known for its rapid production cycle, making it an ideal choice for industries requiring quick turnaround times. This efficiency is particularly beneficial for meeting market demands and reducing time-to-market for new products.
Challenges of Micro-Injection Molding:
1. Tooling Complexity:
Achieving precision on a micro-scale requires intricate tooling designs. The production of molds for micro-injection molding can be complex and costly due to the small size and intricate details of the parts being manufactured.
2. Quality Control:
Quality control becomes more challenging as the components get smaller. Ensuring consistency in part dimensions and properties demands advanced inspection and quality assurance techniques. One way to do that is through process control systems (such as CoPilot).
3. Material Flow and Cooling:
Managing material flow and achieving uniform cooling can be more challenging in micro-injection molding due to the reduced size of the components. Proper design and control measures are crucial to prevent defects and ensure consistent part quality.
4. Limited Material Options for Some Applications:
While micro-injection molding supports a wide range of materials, some specialized applications may require materials that are not suitable for the process. Manufacturers must carefully select materials that meet both size and performance criteria.
5. High-Cavitation Tools:
Micro-injection molding is often tied to high-cavitation tools, which bring their own set of challenges. Maintaining a balanced flow of molten plastic to each cavity is crucial for consistent part quality. It’s also vital to ensure that all cavities are filled simultaneously and uniformly, without creating defects like air traps or voids, which is a complex task to say the least.
6. Residence Time:
Residence time refers to the time that the molten plastic spends inside the barrel of the injection molding machine before being injected into the mold cavity. This parameter is particularly critical in micro-molding, where small, intricate parts are produced. Improper residence time can lead to material degradation, color and property variations, contamination, and more challenges.
Conclusion
Micro-injection molding stands at the forefront of precision manufacturing, offering a multitude of advantages for industries requiring small, intricate components. While challenges exist, technological advancements and ongoing research continue to address these issues, further enhancing the capabilities of micro-injection molding. Using technology, such as process control systems and cavity pressure sensors can help combat the challenges that arise from micro-molding. Need help with you’re micro-molding? We’re here!